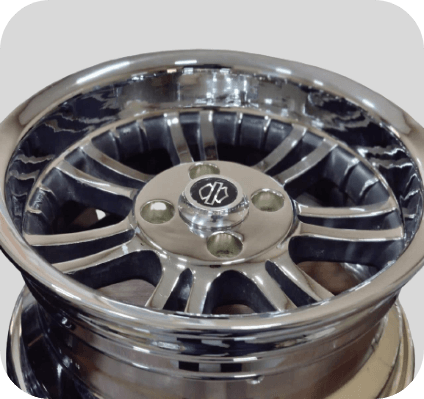
For several metal finishing purposes, chrome plating remains the preferred coating. Despite rivalry from other finishes, including organic coatings and vapor deposition, demand for chrome’s bright and lustrous appearance is still rising.
Due to its unrivaled aesthetics, remarkable corrosive strength, multi-substrate capacity, and supply-chain elements, including massive scale, a large established applicator base, and a long application experience and history, chromium has outlasted the difficulties of the competitive market. Chromium is frequently used for decorative and hard-chrome plating in the metal finishing industry.
Decorative Chrome Plating
Due to its extremely high reflectivity, decorative chrome plating has an unmatchable noble aspect with a mirror-like blue shine. The bright chrome plating process involves electroplating pre-polished substrates with copper and nickel first, then a thin layer of chrome to provide the finish.
Black Chrome Plating
Black chrome plating blends a sophisticated rich black color with the high gloss well-known from bright chrome plating. The deposits have a higher level of microporosity than typical chrome plating, which results in superior corrosion resistance.
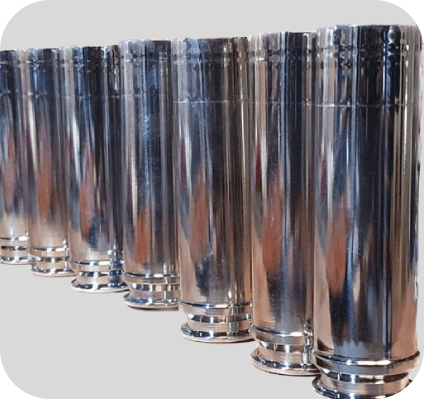
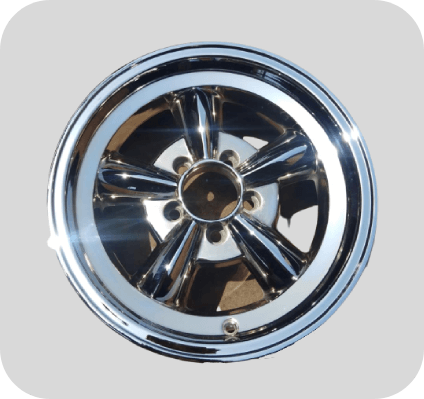
Hard Chrome Plating
The deposit’s nature causes hard chrome plating’s exceptional hardness. The deposit also has an extremely low coefficient of friction. Chrome plating is the ideal layer for wear resistance because it combines these two characteristics with the capability of applying very high thicknesses.
Chrome plating offers several advantages, including efficiency and aesthetics, but a specialist must apply it. Contact a specialist from FMC about chrome surfacing for your equipment if you wish to improve the aesthetics, and reduce aging, wear and tear, friction, or inefficient functioning!!
Standards Followed In FMC
ASTM B650 – Electrodeposited Engineering Chromium Coatings on Ferrous Substrates